I. Introduction
Stainless tube bending is a manufacturing process used to shape stainless steel tubes into various forms, such as curves, angles, or complex shapes, to meet specific design requirements. This process is essential in industries such as automotive, aerospace, construction, and furniture manufacturing, where stainless steel tubes are widely used for their durability, corrosion resistance, and aesthetic appeal.
Understanding the bending process is crucial for industries that rely on stainless steel tubes, as it ensures the production of high-quality components that meet exact specifications. Whether it’s for creating structural components, exhaust systems, or decorative elements, knowing how to bend stainless steel tubes correctly can result in cost-effective production, improved efficiency, and superior end products.
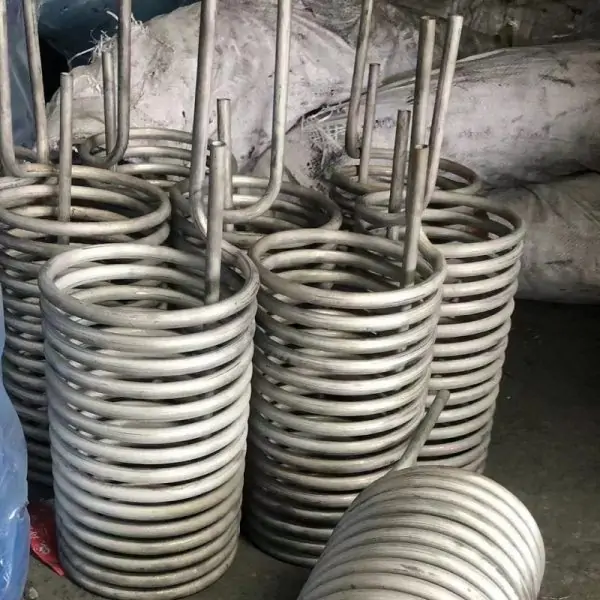
II. Basics of Stainless Steel Tubes
Stainless steel is a steel alloy containing chromium, which provides corrosion resistance and strength. It is commonly used in various industries due to its durability, high-temperature resistance, and aesthetic appeal. When it comes to bending stainless steel tubes, understanding the properties of the material is crucial for achieving the desired results.
There are several types of stainless steel tubes commonly used in bending, including:
-
Austenitic Stainless Steel: This type of stainless steel is the most common and offers good formability and weldability. It is often used in applications requiring high corrosion resistance.
-
Ferritic Stainless Steel: Ferritic stainless steel is magnetic and offers good corrosion resistance in certain environments. However, it is less formable than austenitic stainless steel.
-
Martensitic Stainless Steel: Martensitic stainless steel is strong and hard but has lower corrosion resistance compared to austenitic and ferritic stainless steels. It is often used in applications where strength and hardness are important.
-
Duplex Stainless Steel: Duplex stainless steel offers a combination of high strength and good corrosion resistance. It is often used in applications where both properties are required.
Understanding the properties of these stainless steel types is essential for selecting the right material for bending applications and ensuring that the bending process is carried out effectively.
III. Equipment and Tools
Stainless tube bending requires specialized equipment and tools to ensure precision and quality in the bending process. The following are key components used in stainless tube bending:
- Tube Bending Machine: This is the primary equipment used to bend stainless steel tubes. There are different types of tube bending machines available, including manual, semi-automatic, and fully automatic machines. These machines use various methods such as rotary draw bending, mandrel bending, or compression bending to achieve the desired bend radius and angle.
- Mandrels: Mandrels are used to support the inner surface of the tube during bending, preventing wrinkling or collapsing. They come in different shapes and sizes to accommodate different tube diameters and bending requirements.
- Dies: Dies are used to form the tube around the bend radius. They come in various sizes and shapes to create different bend angles and radii.
- Wiper Dies: Wiper dies are used to prevent wrinkles and ensure a smooth bend surface. They are placed behind the bend die and help maintain the shape of the tube during bending.
- Clamp Dies: Clamp dies are used to hold the tube in place during bending. They ensure that the tube does not move or deform during the bending process.
- Lubrication System: A lubrication system is used to reduce friction between the tube and the bending machine components, ensuring smooth bending and preventing tube damage.
Selecting the right equipment and tools for stainless tube bending is crucial for achieving precise and high-quality bends. It is important to consider factors such as the material of the tube, the desired bend radius and angle, and the production volume when selecting equipment. Using high-quality equipment and tools can help improve efficiency, reduce waste, and ensure consistent bend quality.
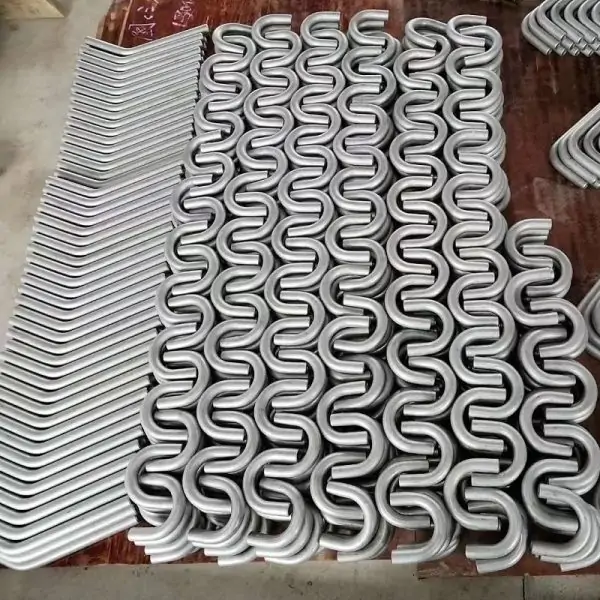
IV. Process Steps
Stainless tube bending involves several key steps to ensure the proper bending of the tube and the quality of the final product:
-
Preparation of the Tube: The process begins with preparing the stainless steel tube for bending. This includes cutting the tube to the required length and deburring the edges to remove any sharp or uneven edges that could affect the bending process.
-
Selection of Bending Method: Next, the appropriate bending method is selected based on the specifications of the project and the desired bend radius and angle. Common bending methods for stainless steel tubes include mandrel bending, press bending, and rotary draw bending.
-
Bending Process: The tube is then placed in the bending machine, and the bending process is carried out. In mandrel bending, a mandrel is inserted into the tube to support the inner wall and prevent collapsing or wrinkling. Press bending uses a press to bend the tube around a die, while rotary draw bending uses a rotating die to bend the tube.
-
Heat Application (if necessary): In some cases, heat may be applied to the tube during the bending process to make it more malleable and easier to bend. Heat can help reduce the risk of cracking or other defects in the bend.
-
Quality Control Measures: Throughout the bending process, quality control measures are implemented to ensure the accuracy and consistency of the bends. This may include monitoring the bend angle and radius, inspecting the tube for defects, and making adjustments as necessary to maintain quality standards.
By following these process steps, manufacturers can ensure the precise bending of stainless steel tubes and the production of high-quality products that meet the required specifications.
V. Factors Affecting Bending
-
Material Considerations: The grade and thickness of the stainless steel tube significantly impact the bending process. Higher grades and thicker tubes require more force and may be more prone to cracking or deformation during bending.
-
Tube Geometry and Dimensions: The diameter, wall thickness, and overall geometry of the tube influence the bending process. Tubes with smaller diameters or thinner walls are generally easier to bend than larger or thicker tubes.
-
Bending Radius and Angle Requirements: The desired bend radius and angle dictate the bending method and machinery needed. Sharp bends or tight radii may require specialized equipment or mandrel bending to prevent tube distortion.
-
Effects of Temperature and Pressure on Bending: In some cases, heat may be applied to the tube during bending to reduce its stiffness and improve formability. However, excessive heat can weaken the stainless steel and affect its corrosion resistance. Pressure can also be applied to help shape the tube, but care must be taken to avoid overloading the material.
Understanding these factors is crucial for achieving the desired bend quality and avoiding defects such as cracking, wrinkling, or springback. By carefully considering these factors, manufacturers can ensure the successful bending of stainless steel tubes for various industrial applications.
VI. Safety Precautions
- Importance of Proper Training and Certification: It is crucial for operators to undergo proper training and certification before engaging in stainless tube bending. This training ensures they understand the equipment, bending process, and safety protocols, reducing the risk of accidents or injuries.
- Use of Personal Protective Equipment (PPE): Operators should wear appropriate PPE, including safety glasses, gloves, and ear protection, to protect against potential hazards such as flying debris, noise, and heat during the bending process. Additionally, ensuring a well-ventilated workspace can help mitigate exposure to fumes or gases produced during bending.
VII. Applications of Stainless Tube Bending
- Examples of Industries and Products: Stainless tube bending is essential in industries such as automotive, aerospace, construction, and manufacturing. It is used to create components for exhaust systems, handrails, hydraulic systems, and structural frameworks, among others.
- Advantages of Stainless Steel: Stainless steel offers several advantages in bending applications. It is highly corrosion-resistant, making it suitable for outdoor and harsh environments. Stainless steel is also durable, with high strength-to-weight ratio, and it can withstand high temperatures and pressures, making it ideal for a wide range of applications.
VIII. Conclusion
Stainless tube bending is a crucial manufacturing process used in various industries to shape stainless steel tubes into desired forms. Understanding the properties of stainless steel and the bending process is essential for achieving high-quality bends. The process involves preparing the tube, selecting the bending method, and ensuring quality control throughout. Factors such as material grade, tube geometry, and bending radius affect the bending process and require careful consideration. Safety precautions, including proper training and the use of PPE, are vital to prevent accidents.
Stainless tube bending finds applications in automotive, aerospace, and construction industries, thanks to stainless steel’s corrosion resistance and durability. As technology advances, future trends may focus on improving precision, efficiency, and automation in the bending process.